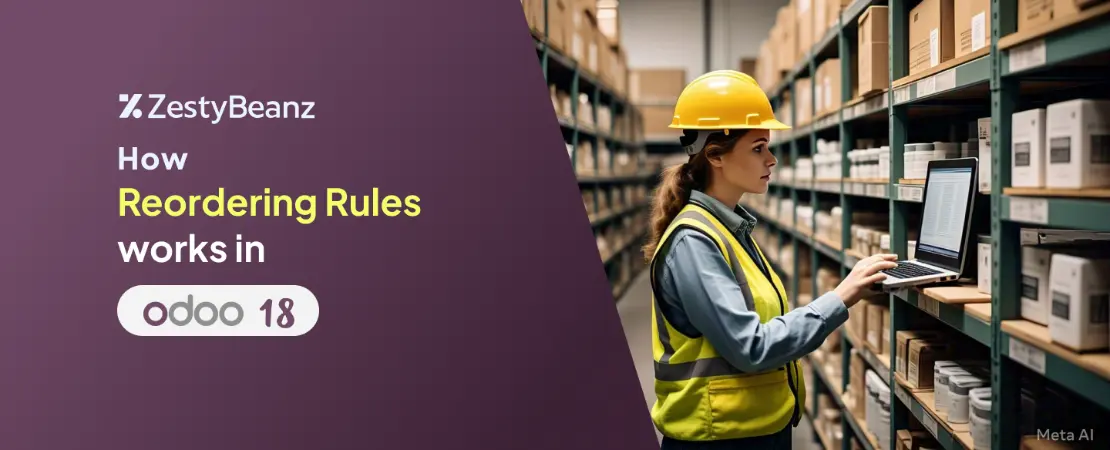
How Reordering Rules Work in Odoo 18
Overview
Reordering rules in Odoo 18 are designed to automate inventory replenishment based on demand and stock levels. They help maintain optimal stock quantities, avoiding overstocking or stockouts. The workflow integrates seamlessly with Odoo’s inventory, purchase, and manufacturing modules.
Workflow of Reordering Rules
1. Configuration:
Navigate to Inventory > Operations > Replenishment.
Setup: Click New and specify:
Product: The item to be replenished.
Location: Where the product is stored.
Min Quantity: The threshold below which replenishment is triggered.
Max Quantity: The desired stock level after replenishment.
To Order: The quantity to replenish.
Unit of Measure (UoM): Measurement unit for the product.
2.Triggering Replenishment:
Automatic Trigger: When the forecasted stock falls below the minimum quantity, Odoo automatically generates a purchase or manufacturing order to replenish the stock.
Manual Trigger: If set to manual, the product appears on the replenishment dashboard for review before initiating replenishment.
3. Replenishment Actions:
Depending on the product’s configuration, Odoo triggers different actions:
Purchase Orders: For products with the "Buy" route, Odoo creates a request for quotation (RFQ) or purchase order to procure the item from a vendor.
Manufacturing Orders: For products with the "Manufacture" route and an associated Bill of Materials (BoM), Odoo generates a manufacturing order.
Internal Transfers: For products sourced from another warehouse location, Odoo creates an internal transfer.
4. Validation and Processing:
Review: Responsible personnel review and validate the generated orders.
Execution: Upon validation, the procurement or manufacturing process proceeds, and stock levels are updated accordingly.
Special Reordering Rule: 0/0/1 Configuration
The 0/0/1 rule is used for products not kept on-hand. Setting Min Quantity = 0, Max Quantity = 0, and To Order = 1 ensures that each sales order triggers replenishment for one unit. Unlike the Make to Order (MTO) route, this method does not reserve stock for a specific sales order but instead triggers an independent replenishment action.
Visibility Days
This setting determines how many days in advance a product appears on the replenishment dashboard before the actual need arises, allowing for better planning and lead time management.
When a product is assigned manual reordering rules, the visibility days setting determines how many days in advance the product will appear on the replenishment dashboard (Inventory app → Operations Replenishment).
To calculate the required visibility days for a product to show up on the dashboard, subtract today’s date from the date when the need for replenishment is expected to appear.
Conclusion
Reordering rules in Odoo 18 provide an efficient framework for automating stock replenishment, aligning with procurement strategies, and streamlining inventory management. By utilizing features such as automatic and manual triggers, internal transfers, the 0/0/1 rule, and visibility days, businesses can optimize stock levels and improve operational efficiency.
If you are looking for an ERP implementation partner with diverse industry experience feel free to contact us. Zesty Beanz Technologies is headquartered in Trivandrum Kerala, We have proven track record of successful implementations across the world in various sectors including Odoo for Manufacturing, Odoo for Trading, Odoo for FMCG, Odoo for Oil & Gas, Odoo for Diary, Odoo for Pharma, Odoo for Cosmetic Clinic, Odoo for Contracting Companies, Odoo for HVAC, Odoo for Logistics, Odoo for Automobile, Odoo for Laundry, Odoo for Field Service, Odoo for E-Commerce & many more
ZestyBeanz offers Developer / Consultant outsourcing programs, Chat with us in Whatsapp and Hire Odoo Developers, Mobile Application Developers, Consultants.
#OdooKerala #OdooKochi #OdooTrivandrum #OdooERP #ProjectManagement #OdooVansales #HireOdooDeveloper